이 같은 성격을 가진 생산부문에 있어서도 한층 더 생산계획에 따라서 생산을 관리 통제하지 않으면 안 된다.
제조능력의 제약조건에 맞는 생산계획이어야 한다.
실현 가능한 권위 있는 계획이어야 한다.
1.3 생산계획이란
「무엇을 몇 개 언제 만드는가?」계획하는 것이다.
販 (시장) 요구를 만족시킨다. = 외부조건
생산활동을 원활하고 효율적으로 한다. = 내부조건
즉,
외 부 조 건
|
|
내 부 요 건
|
* 다 양 화
|
|
* 평 균 생 산
|
* 납 기 단 축
|
|
* 재 고 삭 감
|
* 품 질 향 상
|
|
* 원 가 저 감
|
양자를 어떻게 조화시켜 최종적으로는 어떻게 판매요구에 잘 대응시킬까?
구체적으로는
를 생각 효과적으로 운용해 가지않으면 안된다.
(1) 생산계획은 왜 필요한가
(2) 계획입안의 단위
- 어떤 level의 품목으로 입한하면 좋은가?
「여러분의 공장생산방식은 예측입니까, 수주입니까?」
- 일반적으로 생산형태는 다음의 3가지로 나눌 수 있다.
이같은 개념을 반영한 것으로서 「PM」에 의한 계획입안사고가 나온다.
PM : Production Module
Planning Module
Planning B/M
계획입안 level 품목사양이 특정하지 않을 때 그같은 품목을 Grouping한 품목으로 생산계획을 입안한다. (산세는 후술)
(3) 계획시기, 기간
수주정보
부품정보에 의한 maintenance
혹은 작업부하를 확정하기 위한 maintenance
예를들면 MRP로부터 출력 list
제조일정표
작업구 담당자별 제조일정표
Open Order 일람표등을 사용한다.
상기 < > 내는 처리의 rolling 단위를 나타낸다.
※ 주 생산누계 리드타임과 공장표준 누계리드타임
MRP 용어
예를들면
공장표준누계 lead time은 생산계획입안기간의 목표가 된다.
(1) 생산능력을 어떻게 고려하는가
일반적으로 MRP에서 말하는 사고방식은
※ 주. Capacity 계획 = 작업으로서는 사람계의 작업
계획이 유효하다는 것은 강제력을 가진 것이다.
`강제력을 가지기 위해서는 능력 보증이 필요
능력보증 = 능력 그 자체의 조정
․Dynamic 하게 한다 ⇒ RRP
․단기 능력 조정 ⇒ CRP
잔업
부문간의 조정
응원
shift
인원증가
․생산량의 조정
Input / Output
Output에 맞는 만큼
Input시킬 것
MRP의 System․Support의 기본은
MRP를 돌린 결과를 부하계획으로 Support한다. (MAP)
(일부 Simulation 기능을 가진다)
따라서 PP, RRP 에 대해서 특정한 Support는 하지 않는다.
(MPS가 입력되어 MRP가 돌아가고부터)
생산계획은 생산능력, 부하를 고려한 것을 입안하고 MPS로서 입력해야 한다.
2. MRP와 생산계획
2.1 MRP에서의 생산계획 위치부여
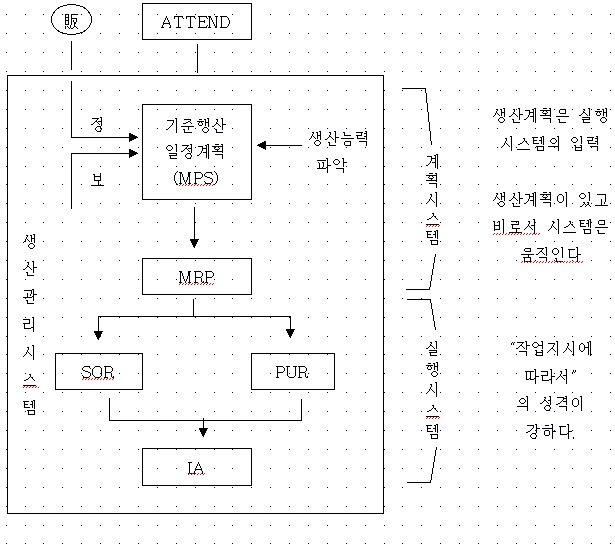
어떻게 계획적으로 움직일 수 있다. System으로 하는가
관리할 수 있다.
GIGO라는 말이 있다.
Garbage - Input Garbage - Output
즉 쓰레기를 넣는다면 쓰레기가 나온다.
2.2 시스템의 유의점
(1) MPS 입력한 날에 MRP 전개한다. (납기회답과 MPS입력은 일체)
우선 입력해 놓고, 후에 실행가능한 계획으로 한다.
--->
메인터넌스가 중요
(2) MPS 입력상의 유의점
日 단위이다.
Dialy bucket = 日 단위 관리
필요일기준 일 것
(3) 부하 축적(적상)
착수일 기준이다.
(4) MPS는 R/D측에서 입력한다.
MPS의 정의
․ 독립소요량이고 구체적인 품번, 수량, 필요일로 나타낸다.
․ MRP 전개의 입력 Data = 생산계획의 개념
․ 생산계획으로서 입력한다.
- 실수주를 따른 계획서
- 선행적 요소를 가진 Dummy 계획
- 선행적 요소를 가진 PM계획
이 MPS가 된다.
※ 주. R/D 입력과 O/D 입력의 차이
(5) PM이란?
① System상의 성격
ⓐ PM으로서 등록된 품번은 그것 자신의 ORDER는 OPEN되지 않는다.
ⓐ 복수제품품번 : 하나의 PM 품번
의 관계는 각 제품품번에서 전개하는 모품목으로서 대상 PM 품번을 결부하는데 따라서 성립한다.
PM의 Grouping
생산공정상의 특성
작업구, 리드타임, ST, 등
총생산량은 어느정도 추정할 수 있지만 그 내역의 사양은 산포(오차)가 있다.
PM으로 입력되어 있는 계획에 대해서 그(引落) 전개하는 모품목을 가진 제품의 실수주가 왔을 때 전표 NO을 입력하면 PM계획이 적용되는 방법
BATCH 처리에 의한 자동인락(전개)
ON-LINE에 의한 인락(전개)
ⓑ Option % 이용
PM으로 Grouping한 제품중에서 각각의 제품 생산량은 산포 동일한 비율이 없을 때 과거의 출하구성비율 또는 사람이 판단하는 장래의 출하구성비율에 따라 Option %를 P/S로 결정됨에 MRP전개에 반영시킨다.
과거 3개월의 출하구성비율에서 Option %의 Maintenance는 System Support하고 있다.
② PM의 P/S구성을 어떻게 하는가?
ⓐ PM Group
공장표준 L/T와 판매 요구 L/T의 차는 어디에 위치 하는가.
혹은 재고전량을 가미하여 중간품을 구성품으로 한다.
부품을 구성품으로 한다.
ⓑ PM Group 각 제품의 부품공용도가 높은 것을 구성품으로 한다.
공용도가 상당히 낮은 부품에 대해서는 개별수배의 방법이 재고를 생각했을 때 Merit 있다고 할 수 있다
ⓒ 리드타임과의 균형
④ PM의 Data 등록에 대해서
ⓐ PIM PDDB의 등록
품목식별 Data
품목구분 「5」
분류 CODE 「PM」
품목내용 「PM Group 명칭」
가명품목명칭 「성공생산 Group」
구성품목 Data
구성품목구분 「0」 --- Option
ⓑ 공장 PDDB에의 등록
품목 Data(ITMDAT)
리드타임코드 「M」
생산리드타임 PM을 가진 사양의 최장 L/T
선행수배용 B/M 「Y」--- Open하지 않는다.
구성품목 Data(PRODST)
사용확률 -------------- Option %
5. PM 삭제
PM이 R/D는 Parameter 일부착 혹은 PM마다의 삭제기간에 따라서 System을
삭제한다.(주차)
따라서 운용상에 있어서 삭제되기 전에 그대로 삭제하느냐?
Dummy order로서 계획하는냐 판단이 필요하다.
2.3 MRP에서의 생산계획 입안을 위한 순서
(1) 생산계획 입안방침의 결정
① 생산누계 L/T과 판매요구 L/T의 차를 안다
ⓐ 각각의 부품리드타임 검증
Support list
P품목 ---- 발주선품목 일람표
M품목 --- 한정부품 리스트
ⓑ 생산누계 L/T 적상계산을 행한다.
ⓒ 판매요구 L/T을 안다.
ⓓ 판매요구 L/T이상의 생산누계 L/T품번을 골라낸다.
MRP에 따라서 (한정부품 LIST)
해당 품번에 대해서 그 내역명세서를 조사한다.
ⓔ 대책의 검토
ㄱ. 조사결과에 근거 문제품목의 리드타임 재검토
ㄴ. 안전재고로 커버하는가
→ 그 결과를 공장표준누계 L/T으로서 적상 販 요구 L/T을 넘는 부품이 있는가
ㄷ. 계획기간의 결정
2. 생산계획의 단위를 무엇으로 하는가, 결정한다.
내역명세를 안다.
PM으로서 입안해야하는 것 ----- P/S 데이터 작성, 등록
Dummy 계획으로서 입안해야 하는 것 ---- 수주량이 많으면 예측되는 표준사양
장납기 부품에 대해서
장납기 부품만의 P/S를 만들고 일괄 선행수배로 하는가 ?
부품개개의 선행수배로 하는가 ?
결정한다.
3. 생산능력의 파악
MRP 운용에 맞춘 생산능력의 파악
특히 Neck 공정에 맞춰 이 제품은, 이 PM은 일당 몇 개의 생산능력인가 파악한다.
4. 기초 Data의 수정
발주방침(뭉치수등)
불량율 등 효율적 생산
제품특성에 맞는 Data인가?
예) 수율 나쁜제품, 소량주문 방지의 고려
작업공정의 보유방식 - 실태와 맞는 공정으로 되어 있는가
(2) 운용순서의 결정
① 생산계획 입력시점에서의 수량결정방법
ⓐ 어느시기에 계획입안하고 입력하는가
예를들면 생판회의등의 販 정보입수시기는?
MRP 시스템으로부터 서포트리스트 출력시기와의 관계는?
ⓑ 수량결정은 무엇을 기준으로 하는가
예를들면 販 정보를 여하히 사용하는가?
실적 Data (과거의 출하실적, 납기별 수주정보)의 이용
공장으로서의 정책 정도 (재고 및 協 포함 부하전략)
→ 이들을 종합적 고려하고 또 반드시 생산회의 등에서 공장으로서 권위가 부여된 것이 중요하다.
② 입안계획의 Maintenance 순서
ⓐ 무엇을 보고 메인터넌스하는가?
장기적으로는 수주동향은 어떻게 되고 있는가?
․ PM 준비상황이 예상이상으로 빠르지 않은가(회답납기가 지정납기보다 늦는 경향이 눈에 뛴다)
․ PM 잔량이 두드러진 경향(실수주가 적다)?
부품의 입수 상황은 당초계획대로 원활한가 (결품발생상황은 어떤가)
ⓑ 단납기, 납기단축 의뢰시의 대응순서
부하 80% 계획이라면 다르지만 100%이상의 계획이면
* 생산능력을 급격히 올릴 수 있는가
ex. 잔업
* 다른 계획(수주분)과의 교체를 생각히지 않으면 안되는
지정출하일과 회답납기의 관계를 고려하면서
* 유사사양제품의 개조도 방법으로 들 수 있다.
case. case대응은 다르지만, 기본순서는 필요하다.
ⓒ 생산계획입안의 책임부문은 어딘가?
ㄱ. Routine으로서 생산계획안 Maintenance의 직접책입부문은 공무부이다.
공무부문은 販 과의 대응에 따라서 그때그때의 시장요구 L/T을 파악하고 한편으로는 자공장 최신의 생산누계 L/T을 파악하고 그 GAP을 어떠한 계획입안 방법으로 메우는가 검토해가지 않으면 안된다. 제조부문, 구매부문이 움직일 수 있는 계획 즉 실현성 있는 어떤 계획을 늘 명심하여 입안하지 않으면 안된다.
ㄴ. 타부문의 움직임
우선 공무입안의 계획에 승인을 하는 일에 따라 준수의무가 일어나는 자부문 담당의 기초 Data를 최신으로 해야한다. (특히 리드타임, S/T등)
GAP이 크면 클수록 계획입안은 어렵고 또 정도도 나쁘기 때문에 메인터넌스 부하가 증가하고 결과적으로는 販 요구에 대응할 수 없다
리드타임의 단축 구매부문 (부품품질향상도 포함하여)
제조부문
기술부문 (작업방법의 개선)
공무가 움직이기 쉬운 환경만들기(조성)을 전부문에서 일치하지 않으면 안된다.
ⓓ 기도입 공장에서의 나쁜 실례
ㄱ. 생산계획은 시스템이 만들어준다.
사람이 만들지 않아도 좋다
특히 부품수배관계에서 발생한 계획이 있어 비로서 MRP
ㄴ. 혼자서 제멋대로 계획, 무리한 계획 부품조달 불가능
고개를 넘어지면서 간다.
미발행오더 누계 = 계획은 엉망진창이 된다.
수복작업에 노력함 = 다음 계획입안도 여가
ㄷ. 공무남자 담당의 MRP 이해가 불충분
결국 SYSTEM은 대응할 수 없음
구매업무와 공무업무와의 성격의 차이?
남자와 여자와 어느쪽이 보수적이라고 생각합니까?
ㄹ. 타부문과의 연대 순서가 약하다.
미발행오더가 점점 쌓여간다.
販 로부터 독촉이 화살처럼 온다.
order의 강제 release를 점점 행한다.
단납기 계획을 입력한다.
구매부문, 제조부문으로부터 불신감을 가지게 된다.
저와 함께 희망을 향해 함께 달리죠.이걸 꾸~욱 누르면서